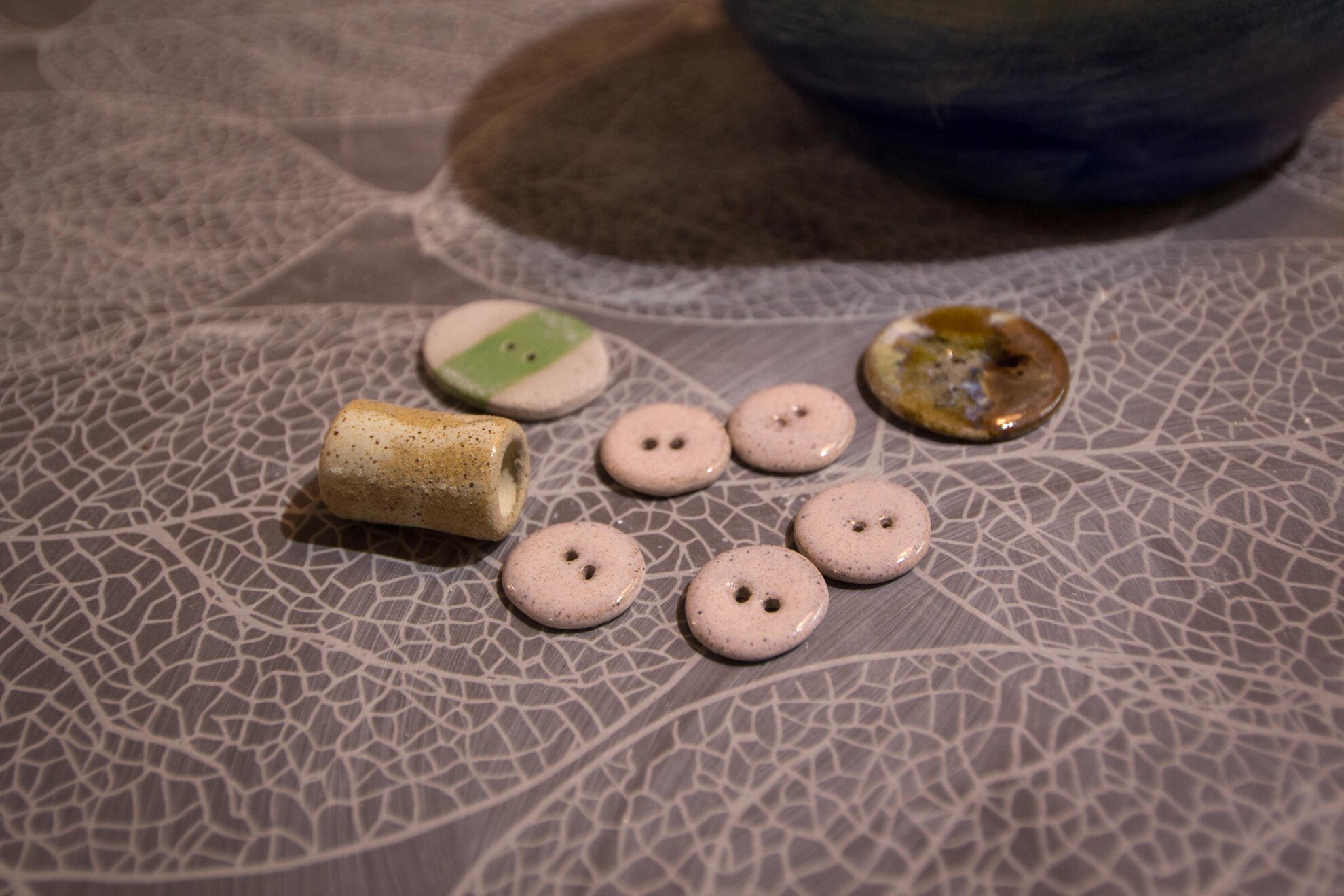
Noha Studios, a Budapest-based ceramics studio, has partnered with the luxury fashion brand Nanushka to create sustainable ceramic buttons which will phase out all the plastic ones currently used in the designer’s collections. The women who make the buttons live in Terény, a tiny village where Natália Nemes, the founder of Noha Studios and head potter, bought a house four years ago.
“When I came here, I started to meet the people,” says Natália. “And there was no work for them in the village.”
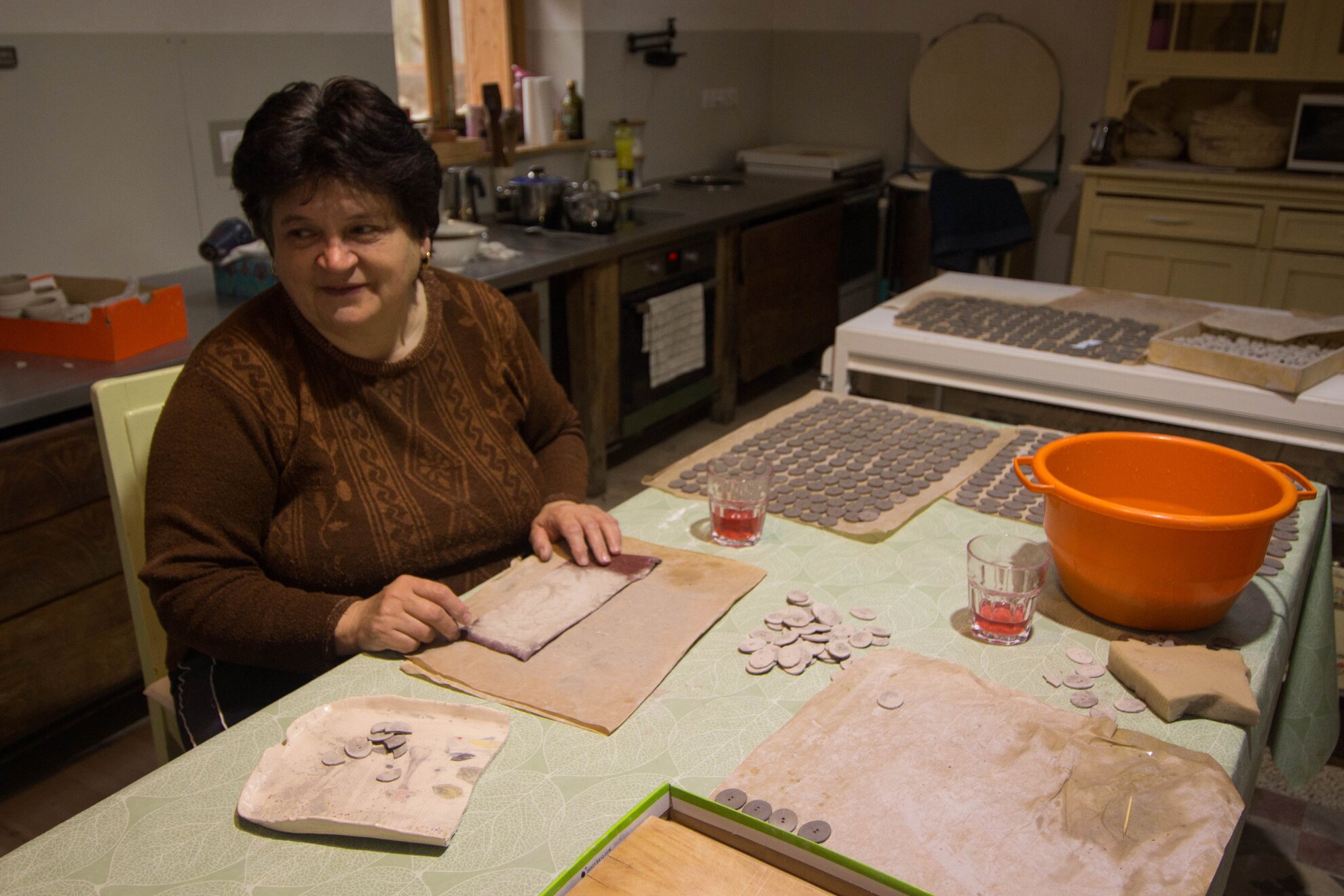
“Especially for women,” chimes in Marika Szilágyi, one of the button makers. She sits across the table from Evi Grenyó, her friend and neighbour. “And if there was work, it paid very poorly,” she adds. “Natália asked if we would like to work for her, and we said yes, because we like to make things by hand.” It was the first time the women had ever worked with clay.
“We have made 10,000 buttons,” says Marika, “or more.” It’s a lot of buttons, each one created individually. “We make them with heart and love.”
Another woman in the project, Ami Nagy, creates rounded beads, which she crafts on a potter’s wheel. Her deft movements make it hard to believe that she hasn’t been doing this for years.
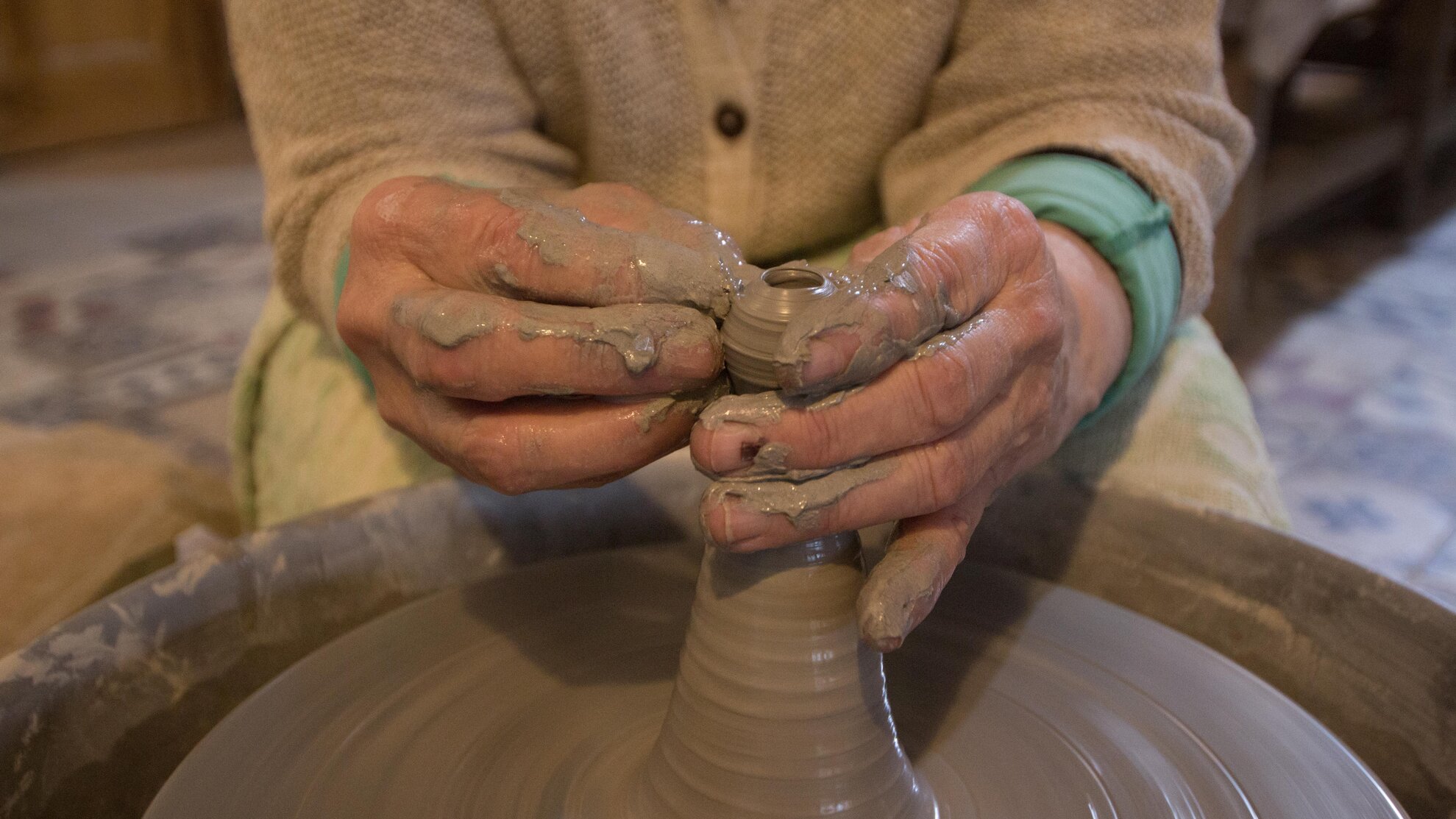
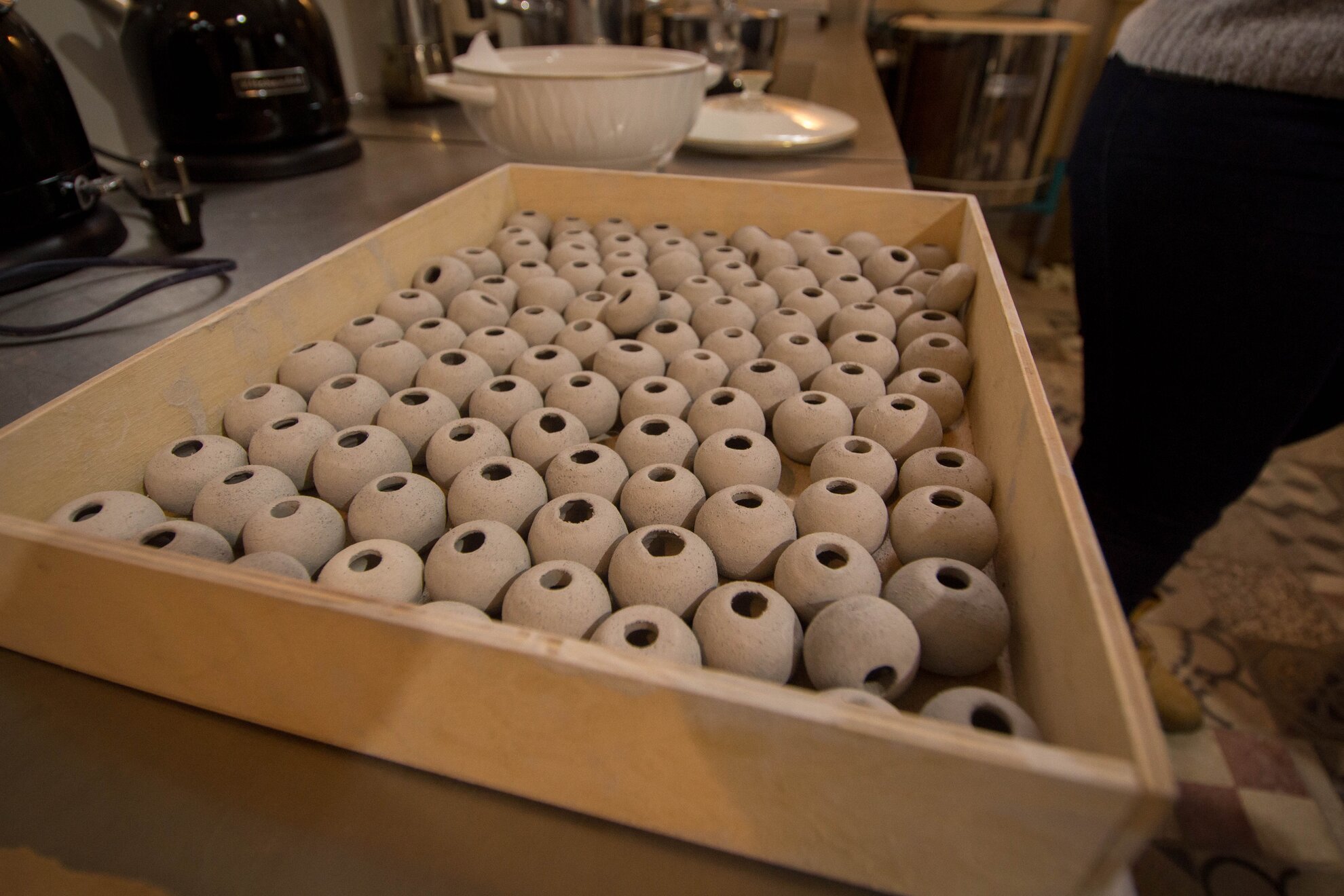
The women demonstrate the process of making the buttons, beginning by rolling a thick slab of clay under a metal roller until it is the right thickness. “We work together on this,” they explain. “Because it’s hard to turn the roller and we want to make sure the clay comes out evenly.”
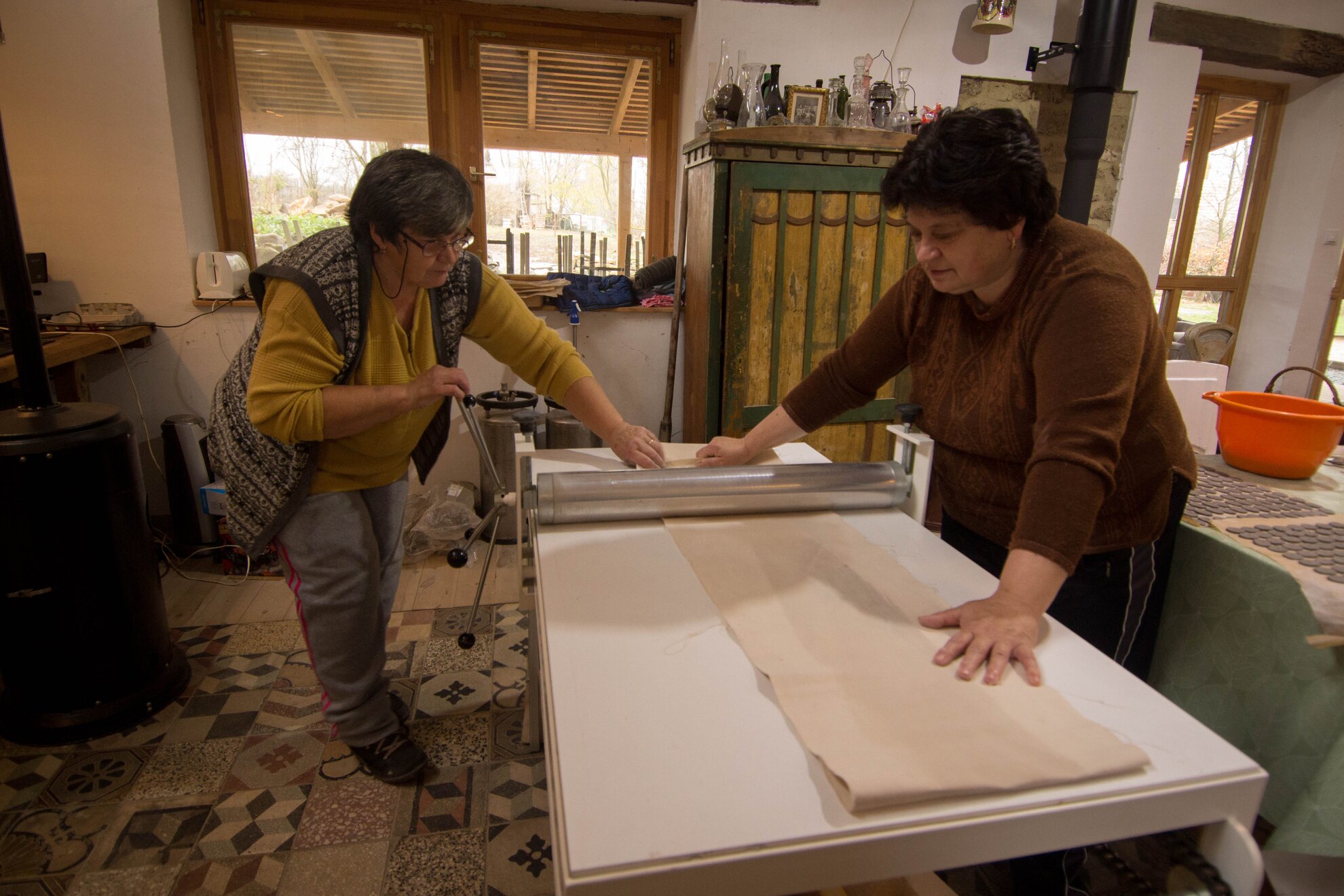
A small, hand-held device punches out the buttons, and pricks a preliminary mark where the holes will go. The last part is created by hand, then the buttons are laid out carefully in front of a small wood-burning stove, to dry and harden. Back at the table, the dry buttons are sanded, the holes are adjusted, and everything is checked for perfection. On occasion the buttons break in this process, as they are delicate and fragile before they’ve been fired in the kiln. In this case, they are soaked in water and thrown back into the raw clay, to be reused.
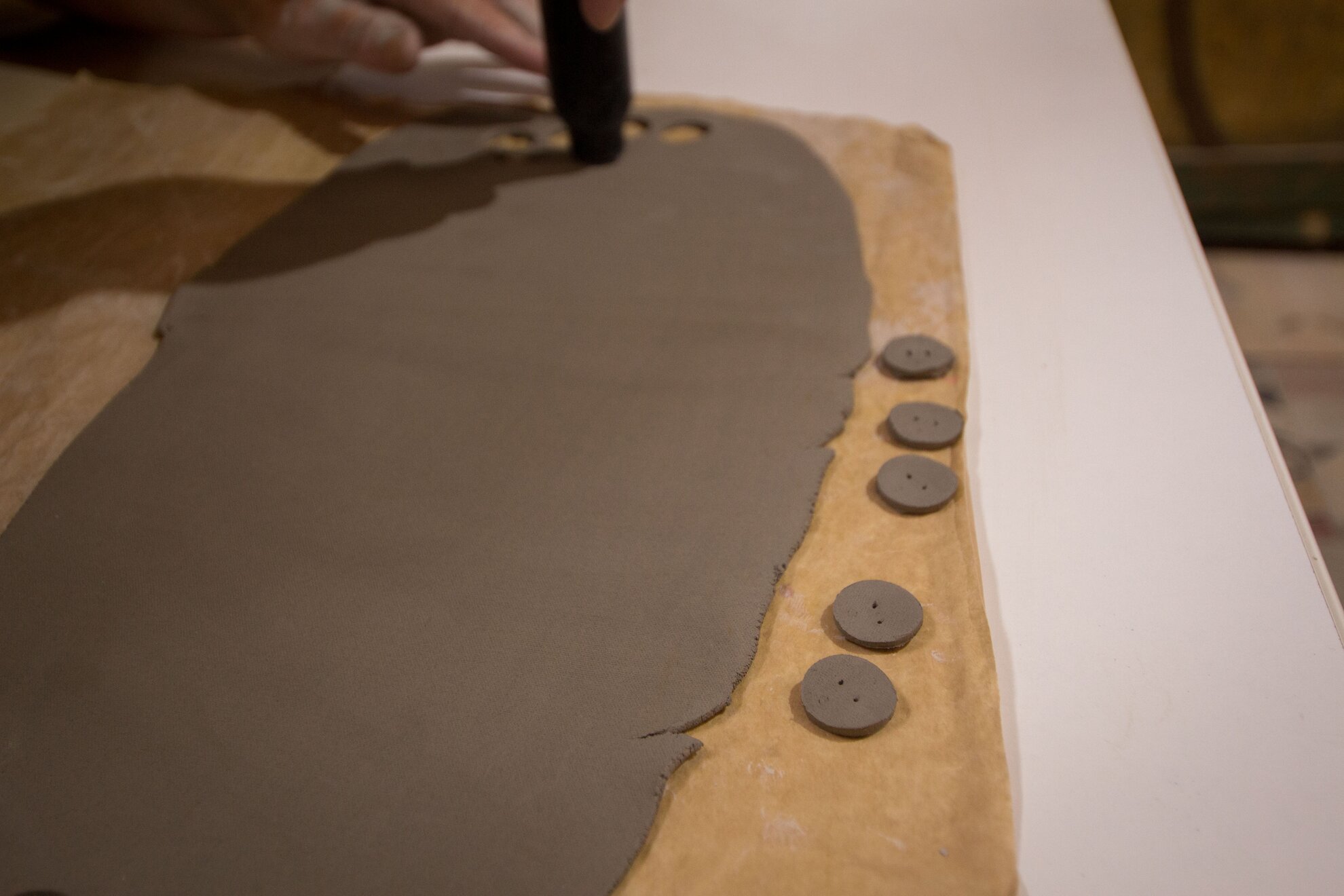
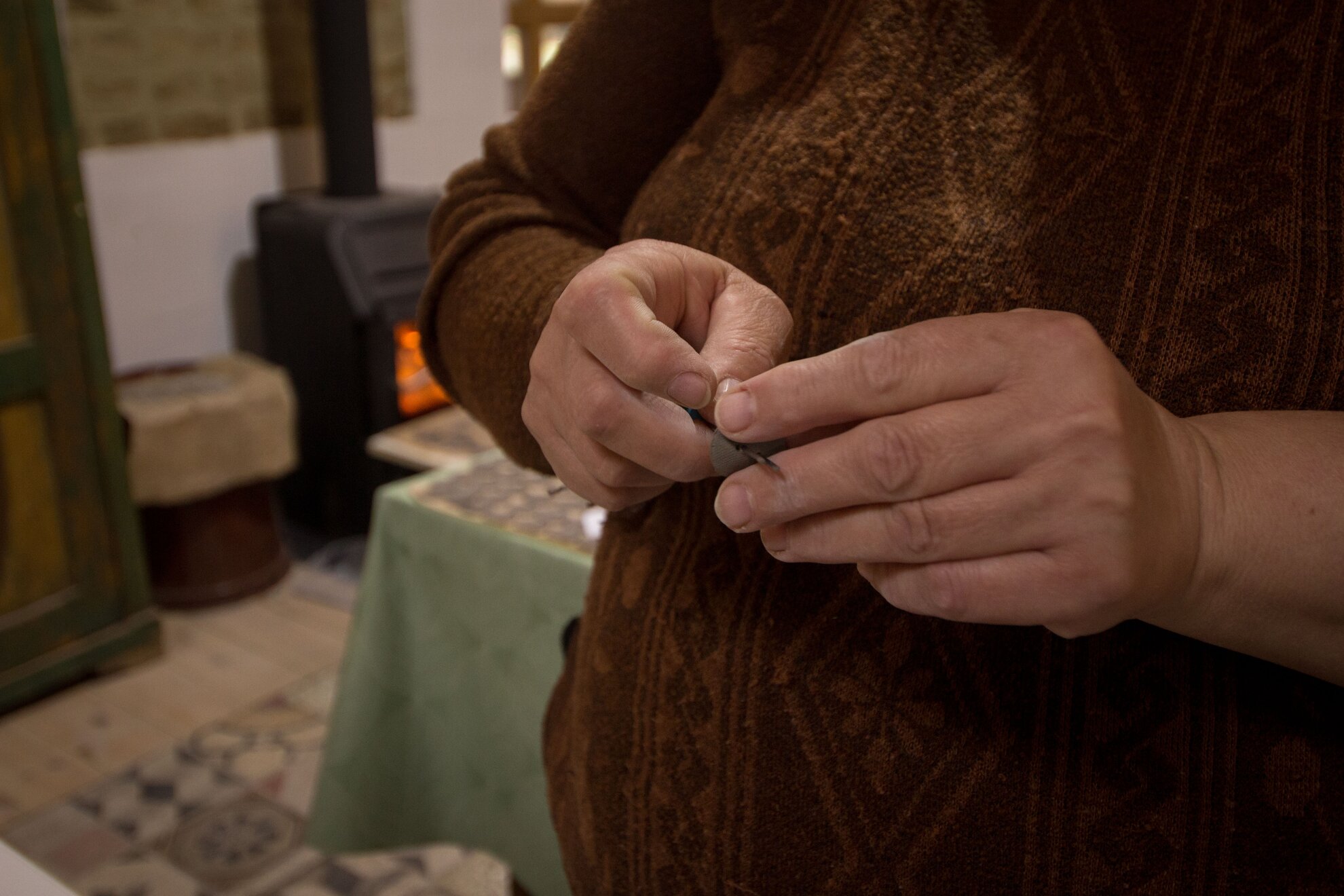
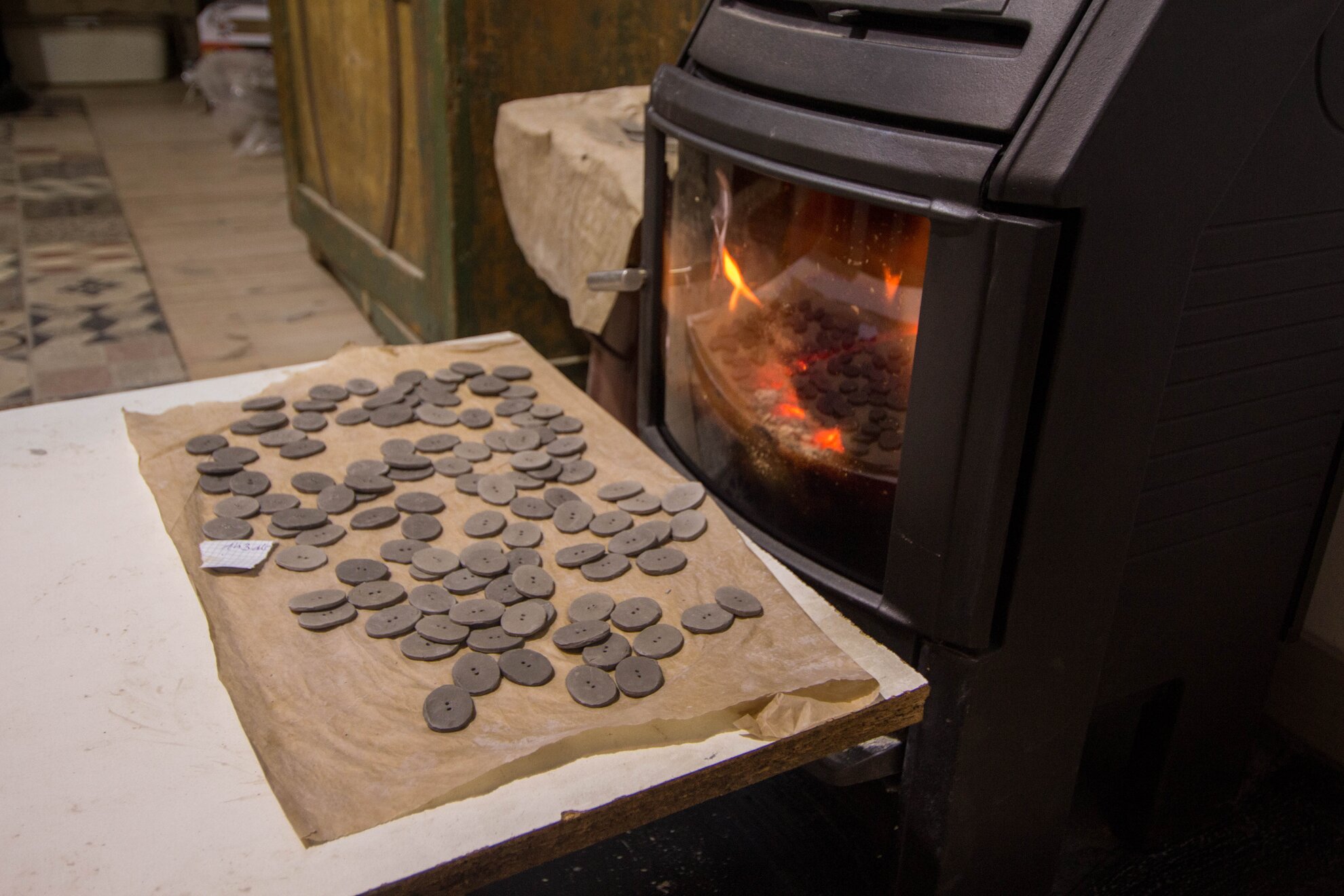
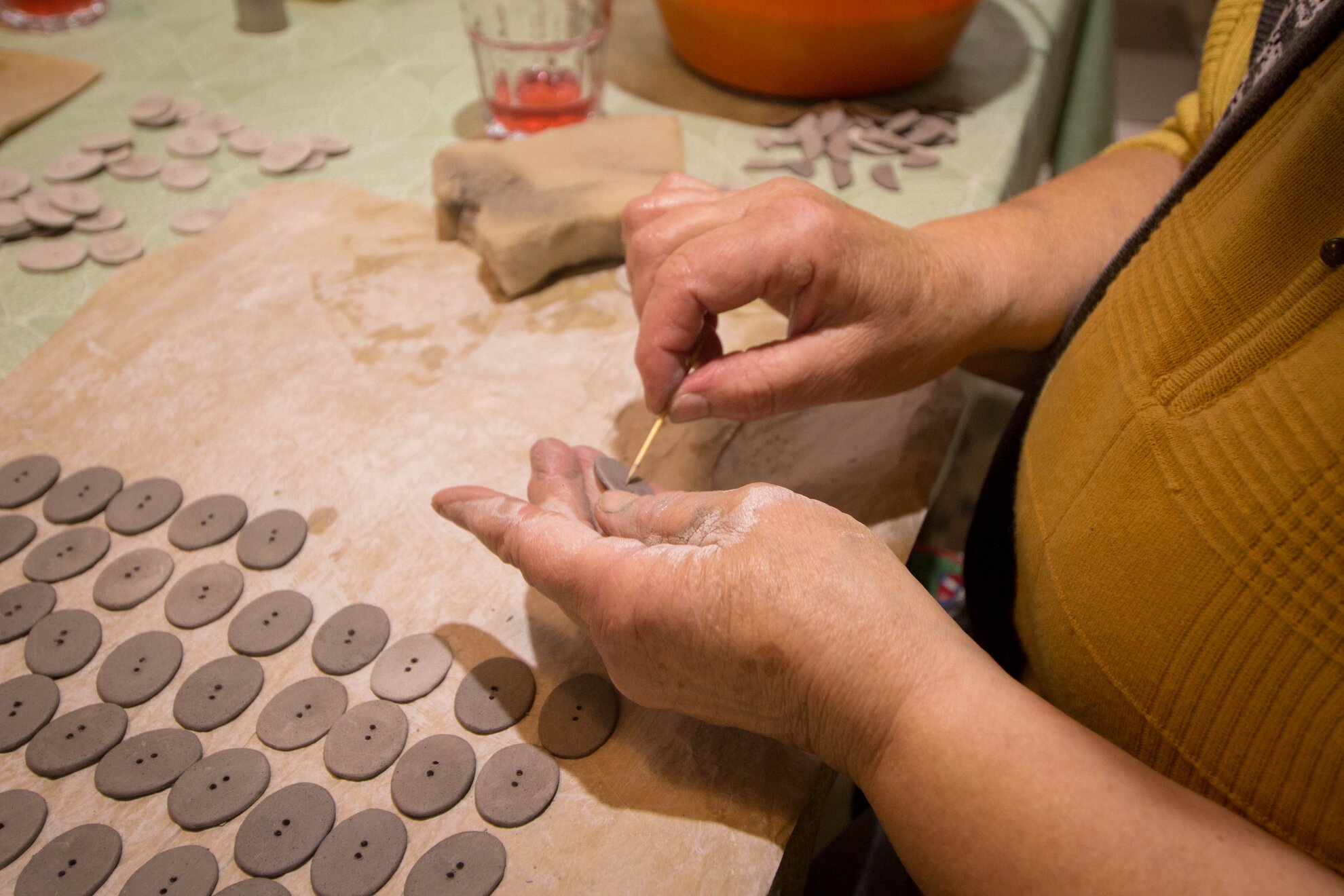
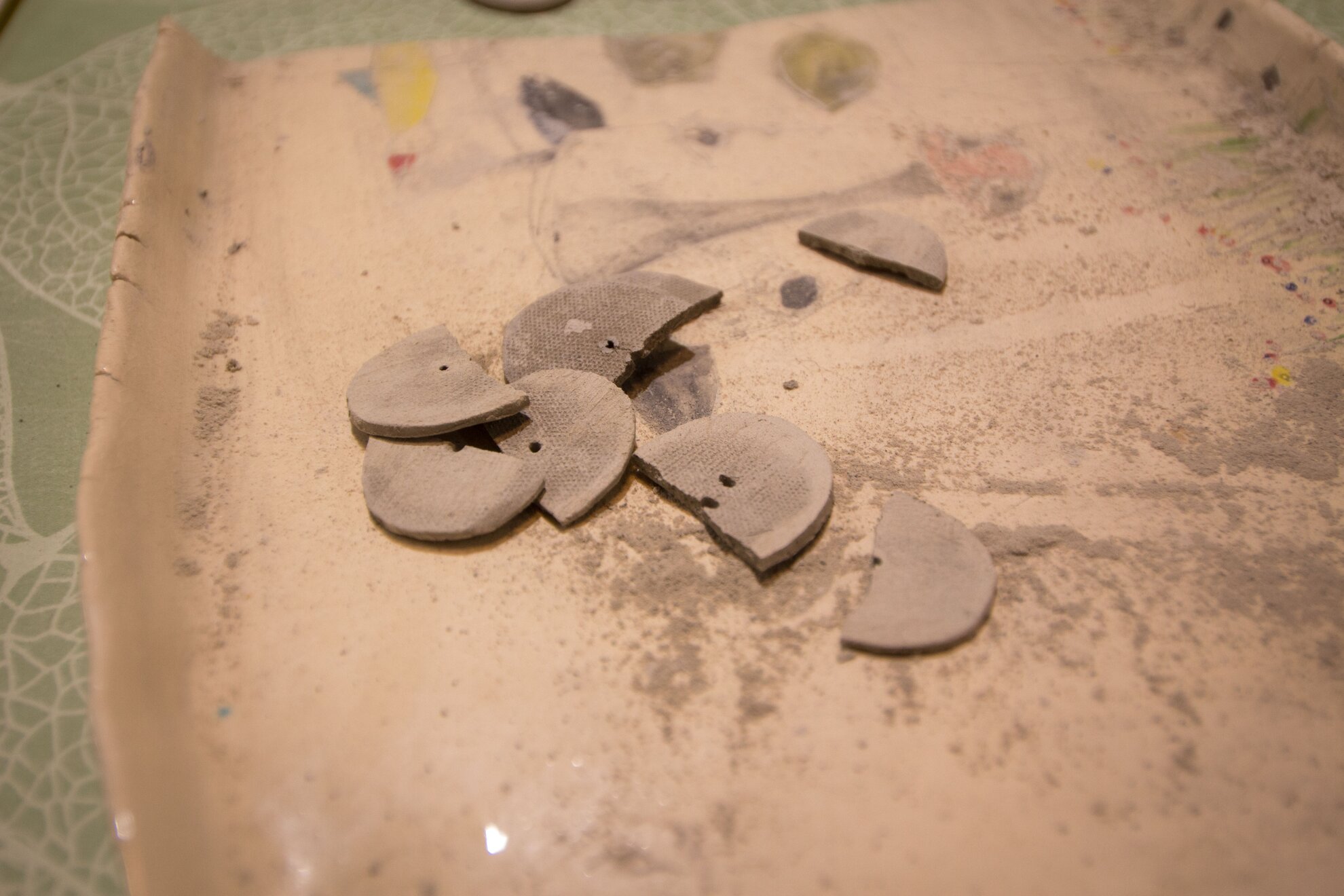
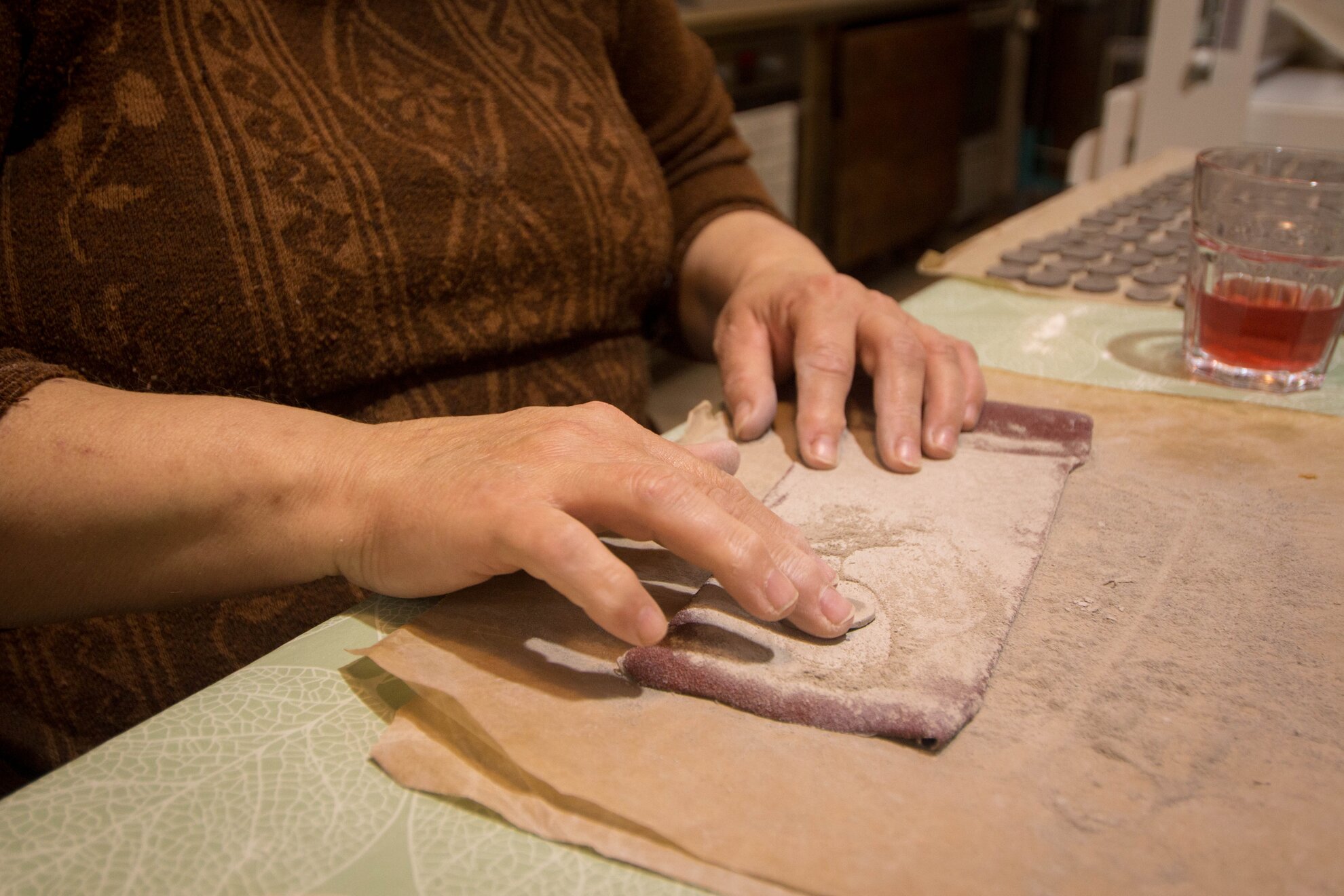
Each button will be handled ten times before it is ready to go in the box.
“We like the process,” says Marika. “And then at the end, when everything is done, we can see what we created. It makes us very proud.”
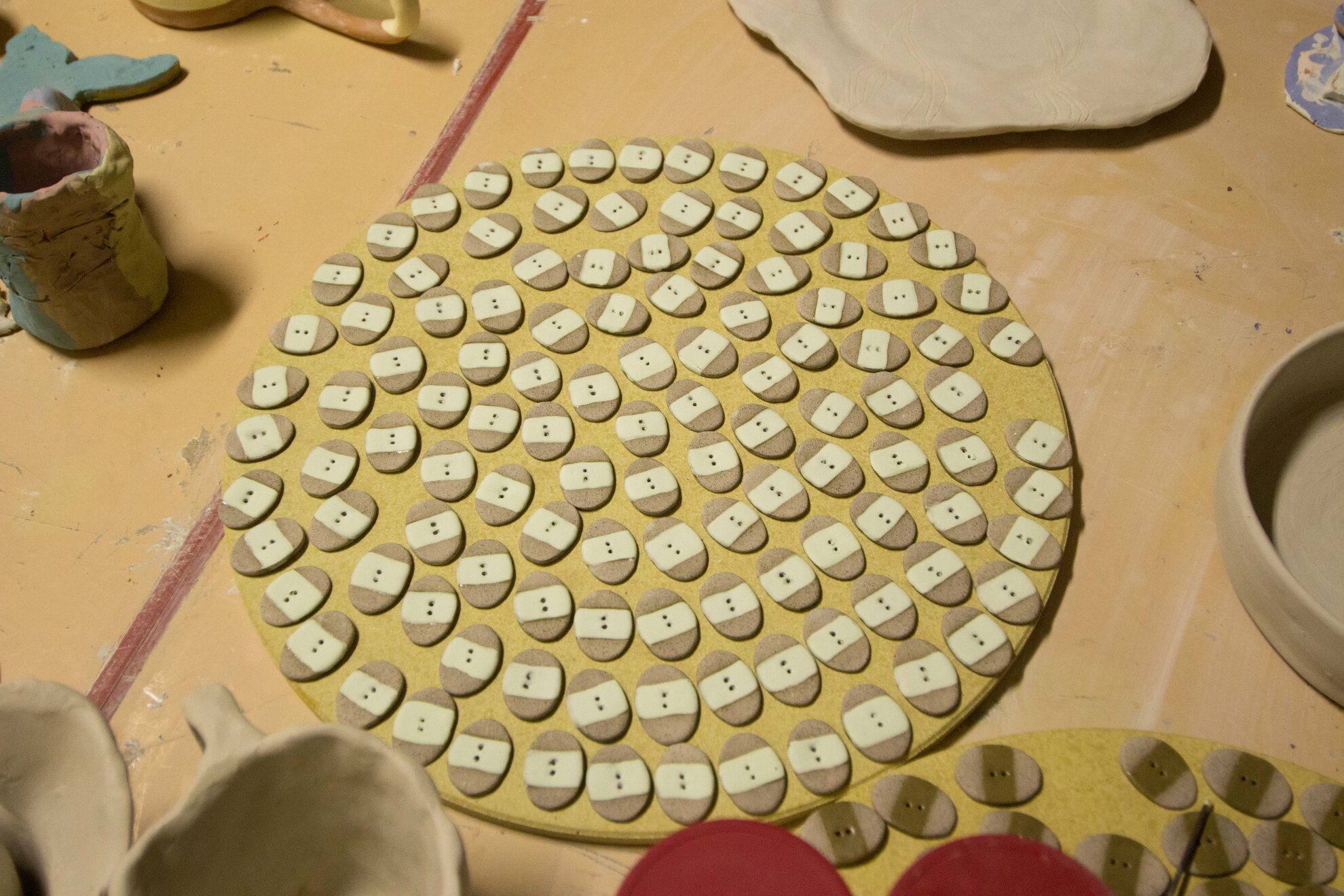